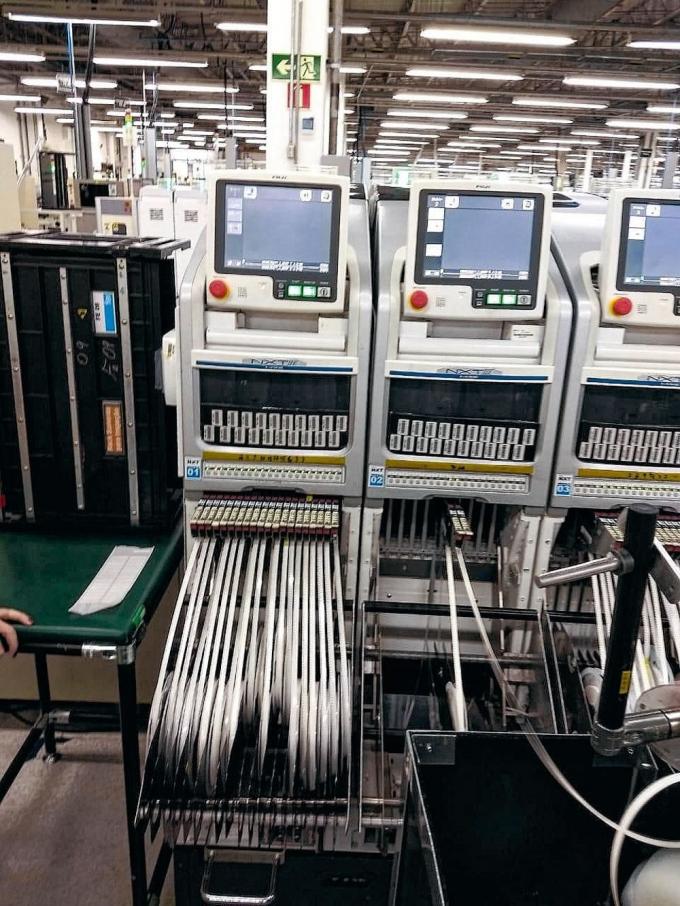
Comment est fabriqué votre smartphone ?
Au cours de l’année écoulée, pas moins de 1,555 milliard de smartphones ont été vendus. Data News s’est rendu chez Huawei et Motorola pour y visiter les lignes de production des P20 et G7.
Nous avons visité Motorola à São Paulo au Brésil, où Motorola fabrique pour le marché d’Amérique latine. Et pour Huawei, nous nous sommes rendus dans leur base de Shenzhen. Bien qu’il s’agisse de deux entreprises différentes situées à deux extrémités du globe, deux éléments nous frappent : les processus de production se ressemblent fortement et ne nécessitent que relativement peu d’intervention humaine. Même si nous avons l’impression que chez Motorola, le travail manuel (de précision) reste un peu plus important.
Entrer dans l’usine n’est pas une sinécure. Les ordinateurs et smartphones doivent être laissés à l’entrée. Nous recevons une veste antistatique et des protections pour chaussures avant de suivre scrupuleusement notre guide à travers les lignes de production. En fait, il s’agit d’un alignement de machines sur quelque 120 m de long. On en compte ainsi 5 par étage chez Huawei. Chaque ligne produit quelque 2.400 appareils par jour dans un cycle de 24 à 38 h et commence par la plaque d’impression. Chez Motorola, on a déjà produit plus de 220 millions d’unités depuis l’ouverture de l’usine en 1996.
La première étape consiste à apposer une solide couche de pâte à souder. Ce faisant, les composants pourront ensuite être positionnés à la machine. Ces éléments, parmi lesquels le processeur, se présentent sur des bobines qui ressemblent fortement à celles des anciens enregistreurs sonores. Une telle bobine contient des centaines de composants identiques qui sont apposés sur la plaque avec une prévision de moins de 0,4 mm. L’inspection optique réalisée ensuite permet de détecter les erreurs et de renvoyer les plaques mal montées au début de la chaîne. A ce niveau, le taux d’erreur dans le processus de fabrication serait plus élevé chez Motorola, précisément parce qu’il s’agit de l’opération la plus précise de l’ensemble de l’assemblage.
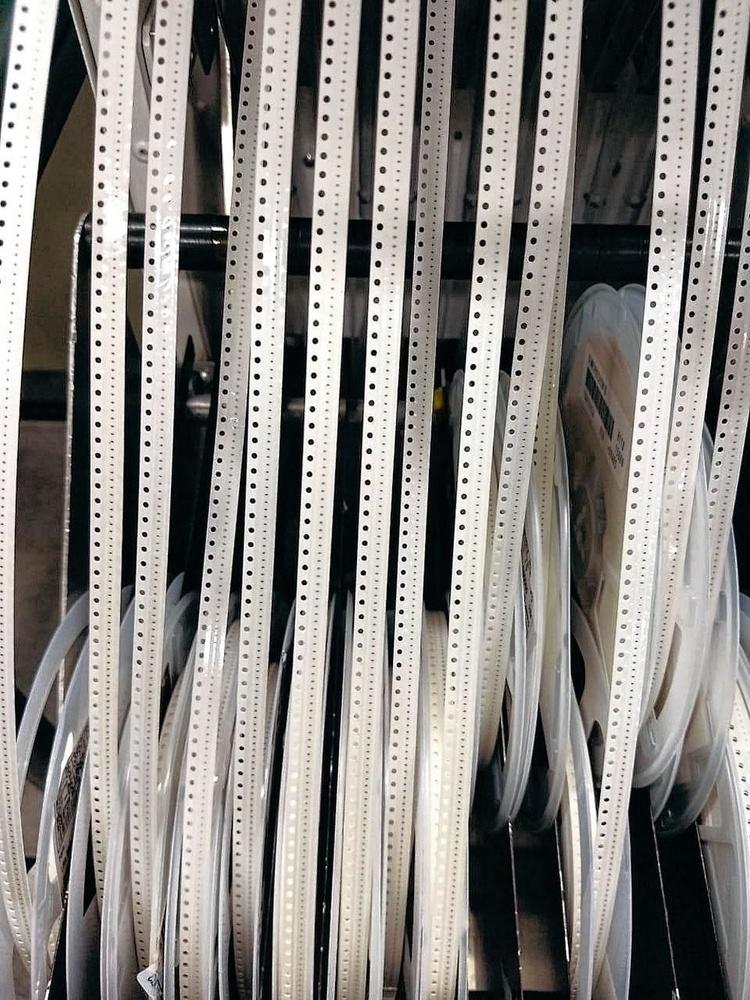
En revanche, chez Huawei, le module de caméra n’est pas installé mécaniquement. Les smartphones sont sortis de la chaîne et un ouvrier place alors un petit bloc qui contient notamment les lentilles de la caméra. Par contre, le bloc est fixé à l’aide de vis par une machine.
Une chaîne de production est occupée en moyenne par 17 ouvriers. L’entreprise cherche à automatiser au maximum la fabrication. Voici un peu plus de 5 ans en effet, on comptait encore 80 personnes par ligne. ” Nous investissons beaucoup dans la poursuite de l’automatisation “, explique Paulo Caixeta, ingénieur produit chez Motorola Mobility. L’usine emploie aujourd’hui 5.500 personnes – y compris la R&D, le prototypage, la distribution, le service et la réparation.
L’automatisation poussée se remarque d’ailleurs également au niveau du centre de distribution de Huawei. L’ensemble du site de production, où sont également fabriqués les routeurs et d’autres matériels, ne nécessite que 145 personnes. Les composants sont retirés mécaniquement des étagères de plusieurs mètres de hauteur et acheminées vers l’unité d’assemble à l’aide de petits robots. Et les produits finis sont transportés par ces mêmes robots ou par bande transporteuse vers leur destination finale.
S’il y a à première vue pas mal de similitudes entre les processus de fabrication chez Motorola et Huawei, le constructeur chinois nous fait comprendre qu’une grande partie des machines a été conçue en interne. Ce qui, aux dires de Huawei, permettrait un assemblage de meilleure qualité. Pour sa part, Motorola précise que pour de nombreuses tâches d’automatisation, elle fait appel à des entreprises brésiliennes (de robotique).
Tests
En théorie, un smartphone peut rester durant 24 h sur la chaîne d’assemblage. Mais en pratique, ce délai peut être 2 fois plus long. En cause, le fait qu’entre les différentes phases, des tests sont régulièrement menés. C’est ainsi qu’avant même que le boîtier soit posé autour de l’appareil, le téléphone est retiré de la chaîne par un robot et placé dans un tiroir afin de tester notamment s’il résiste à de hautes températures ainsi que de vérifier s’il n’y a pas de problème dans l’émission de fréquences.
Au terme de ces tests, les appareils sont remis automatiquement sur la ligne de production. Avec en plus certains codes QR, lesquels sont surtout destinés au contrôle de qualité. S’il devait y avoir ultérieurement un problème avec un appareil, Huawei pourrait dire avec précision de quel lot et composant il s’agit, ce qui permettrait de mieux isoler le problème du reste de la production.
Une fois que le matériel interne est testé, l’écran est ajouté. Cet écran est en fait pressé durant 2 h sur l’armature de l’appareil. Après quoi le smartphone reste encore durant 10 h environ au repos pour améliorer encore la stabilité. Par la suite, le boîtier et la batterie sont ajoutés, le téléphone étant de facto terminé.
Vient ensuite le test de ‘burning’ : l’appareil est à nouveau testé à une température de 30° C, cette fois pas uniquement au niveau des fréquences, mais de l’ensemble des composants. Pour ce faire, l’appareil est activé et tant le matériel que le logiciel sont mis en charge.
Le processus présente-t-il souvent des erreurs ? Assez rarement. Huawei estime que le nombre de composants défaillants dans le processus d’assemblage n’est que de 2,87 sur 1 million. Certes, il ne s’agit là que du processus d’assemblage, donc hors production du processeur, de la batterie et des autres éléments. Ajoutons que Huawei, à l’instar d’Apple et de Samsung, fabrique elle-même ses processeurs. Pour sa part, Motorola fait actuellement appel aux processeurs de Qualcomm.
Le module sonore, la batterie et la caméra sont testés séparément. A noter que chez Huawei, le son est largement testé de manière manuelle. Les téléphones sont placés dans de petites pièces (presque) insonorisées où un ouvrier vérifie si le son est correct. Il s’agit d’ailleurs là du seul endroit où un ouvrier peut s’asseoir. Précisons encore que chez Motorola, le travail ‘fin’ est confié littéralement à de ‘petites mains’ puisque la grande majorité du personnel est féminin. Pas étonnant, explique Motorola : ” La main de la plupart des hommes est simplement trop grande pour effectuer ce travail de précision. ”
Si l’appareil réussit ce test, il est prêt à être emballé. Le téléphone est placé dans une boîte qui comprend aussi les manuels, le chargeur et des accessoires éventuels.
La dernière étape enfin est le passage sur la balance. Ce faisant, le fabricant sait si des éléments sont manquants (ou trop nombreux). Chez Huawei, un smartphone ne peut pas s’écarter de plus de 6 g de son poids idéal, contre à peine 1 g chez Motorola. ” Cela permet même de savoir si la notice de conformité obligatoire est manquante “, nous assure-t-on.
Comment tester un pylône d’émission ?
Outre des smartphones, Huawei fabrique également des pylônes d’émission qui doivent aussi être testés. En l’occurrence, nous avons visité leur Spherical Near Field Test System, un espace fermé de 10 x 12 x 15 m où une station de base peut être testée. Huawei teste chaque nouvelle station de base qu’elle commercialise et 1% de l’ensemble des stations de base commerciales qu’elle expédie.
Sur la photo ci-dessus, la station de base se trouve au centre. L’anneau orange mesure les signaux autour de l’antenne. Cette antenne peut d’ailleurs tourner, ce qui permet à l’anneau de mesurer le signal à 350°. Les 4 pics que l’on voit autour de l’espace sont destinés à neutraliser les signaux. La chambre est conçue de telle manière qu’à l’intérieur, aucun signal provenant de l’extérieur ne puisse être mesuré et inversement, que le pylône d’émission testé n’ait aucune influence sur les activités du reste du bâtiment.
Huawei dispose d’une seule pièce de cette dimension, mais aussi de 2 salles semblables plus petites pour tester d’autres équipements sans fil. La chambre proprement dite a été livrée par la française Satimo.
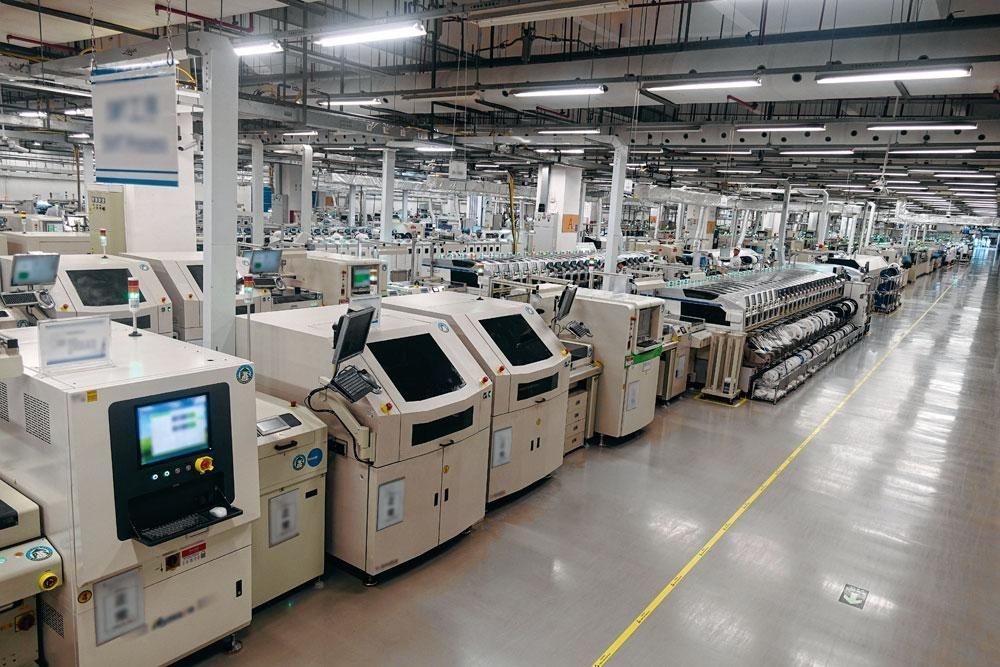
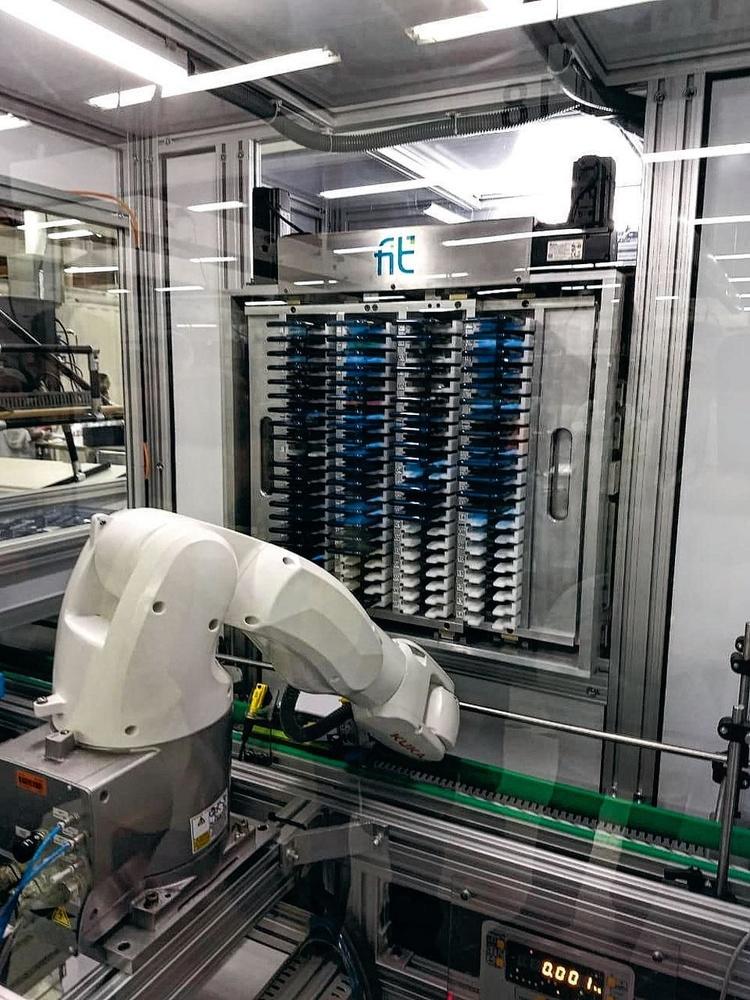
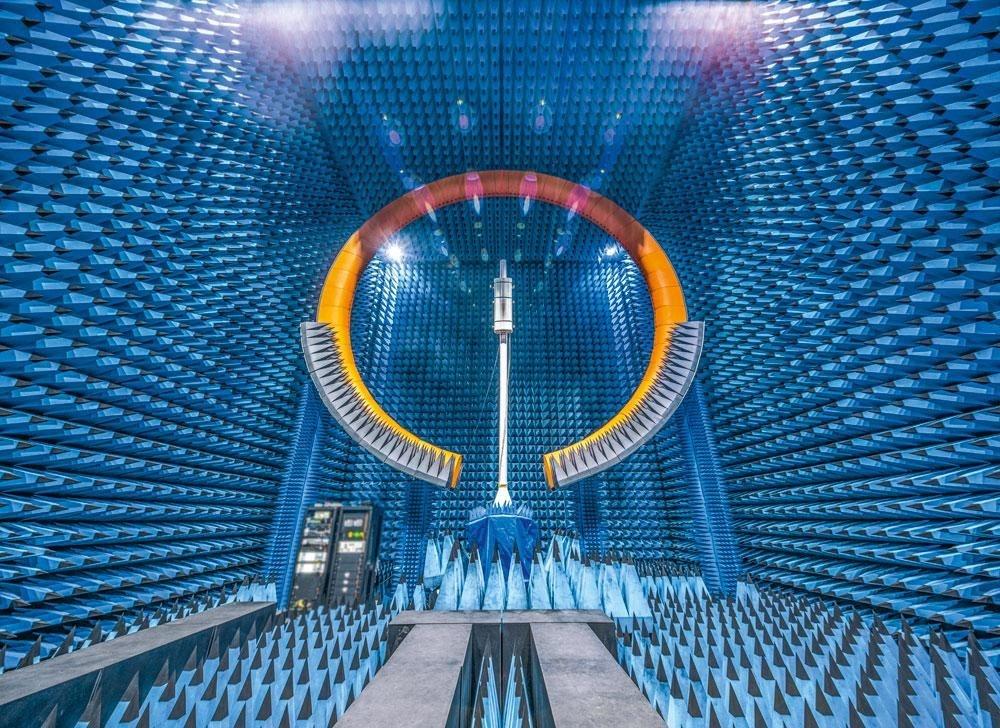
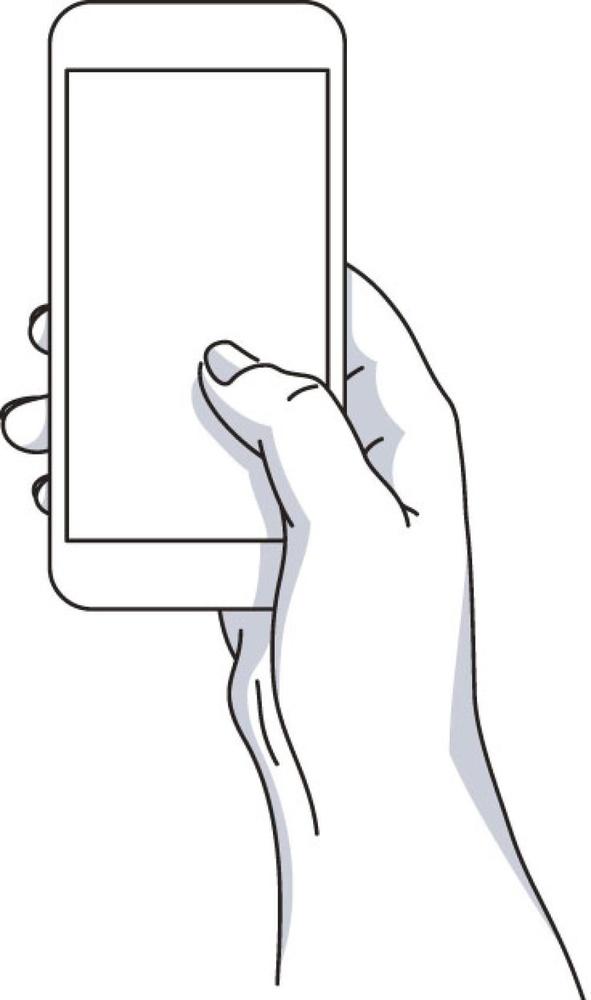
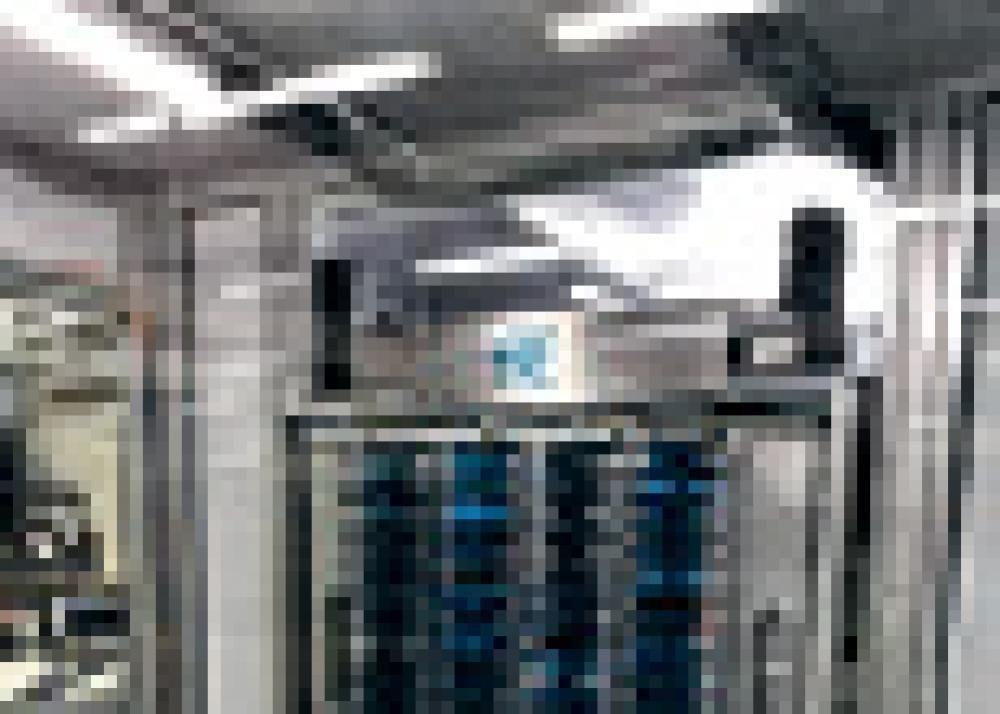
Vous avez repéré une erreur ou disposez de plus d’infos? Signalez-le ici