Le nouveau modèle de la marque de lunettes belge Odette Lunettes est lancé sur le marché comme étant durable, parce qu’il a été créé au moyen de l’impression 3D et avec des matériaux naturels. Mais quel est en réalité son degré de durabilité?
Les lunettes, promues par l’ex-coureur cycliste Tom Boonen, sont fournies par l’entreprise technologique louvaniste Materialise. Cette dernière s’était autrefois fait connaître en pleine vogue ‘imprimez vos propres fichiers 3D’, mais se consacre aujourd’hui à des prototypes pour l’industrie automobile, à de l’équipement médical, à des semelles créées sur mesure, mais aussi donc aux lunettes. Dans ce dernier cas, Materialise imprime les montures, souvent sur mesure. Les verres et les petites vis y sont insérées par la suite.
Quantités réduites
‘Eye wear est l’une des applications qui se prêtent à merveille à la 3D’, déclare Jurgen Laudus, vp et general manager Manufacturing chez Materialise. ‘On peut imprimer des quantités réduites et utiliser des concepts qui ne conviennent peut-être pas aux moules classiques. Le processus est également plus durable, parce qu’il ne faut par exemple pas découper une monture dans un bloc assez volumineux.’
La plupart des lunettes ne sont cependant pas fraisées, mais fabriquées avec un moule dans lequel le plastique est coulé. ‘Cela se fait aussi souvent de l’autre côté de la Terre pour réduire les coûts, ce qui entraîne un risque de stockage’, explique Laudus. En d’autres termes, il convient de vendre de grandes quantités de lunettes pour récupérer le coût de la création de ce type de moule. Et si cela ne marche pas, elles se retrouvent sur la montagne des déchets. La solution proposée par Materialise pour fonctionner de manière plus durable est dès lors très simple: produire moins et localement. ‘Chez nous, il est possible de produire réellement des petites séries: de mille à deux milles pièces. Si la demande est plus importante, on imprime simplement des exemplaires en plus.’
Pour de plus faibles quantités, ce mode de production serait même plus avantageux, précisément parce qu’on économise sur le transport et les surplus. ‘Et la forme ultime de ce genre de mini-série est représentée par des lunettes personnalisées créées à la mesure du visage du client’, ajoute encore Laudus. L’entreprise expérimente entre-temps des systèmes de scannage chez les opticiens, qui enregistrent les dimensions de votre visage, de vos oreilles et de votre nez, afin de vous fournir dans les dix jours un exemplaire personnalisé, sorti tout droit de l’imprimante 3D.
Surplus
Les nouvelles lunettes d’Odette Lunettes exploitent aussi un nouveau type de matériau appelé PA11. ‘Il s’agit d’un nylon à base bio, fabriqué à partir de graines de ricin’, précise Laudus. Le ricin est cultivé en Inde sur un sol pauvre. De l’huile extraite de ses graines, on produit du plastique. Tout cela a pour but de réduire de moitié les émissions de CO2 lors de la fabrication du nylon par rapport aux types de plastique plus traditionnels, qui sont utilisés pour ce modèle d’impression 3D.
Mais qu’en est-il alors du surplus? Les grandes productions d’impression 3D n’utilisent pas, comme le fait la petite imprimante domestique, une variation du système à jet d’encre qui fabrique chaque composant couche par couche avec du plastique injecté. La technologie exploitée ici s’appelle en jargon ‘synthé laser’, à savoir l’impression dans un grand récipient rempli de poudre. ‘Cette poudre est fondue à 180 degrés. Nous chauffons le récipient jusqu’à 170 degrés, puis nous ajoutons de l’énergie au moyen d’un rayon laser, afin de produire la monture’, déclare encore Laudus.
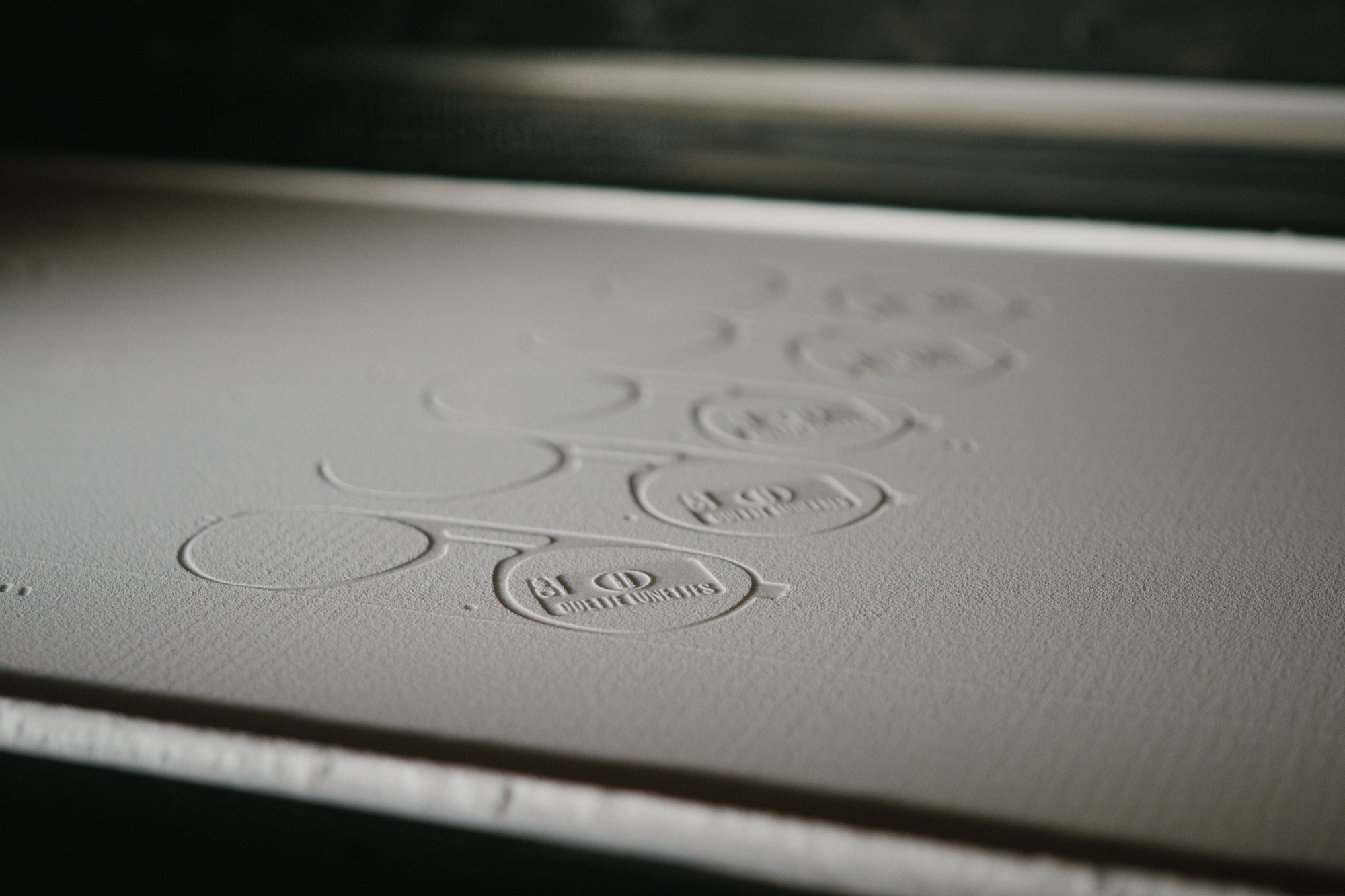
Et Laudus de montrer comment cela se passe dans le hall de l’usine. Dans l’imprimante 3D, une fine couche de poudre blanche est déposée sur une grande plaque. Grâce à un laser, l’imprimante fusionne les éléments ad hoc. La plaque abaisse ensuite un fragment d’un millimètre vers le bas. Une nouvelle couche de poudre y est ensuite déposée, dans laquelle quelques éléments sont de nouveau fondus’. En bout de course, on se retrouve avec un récipient contenant toute une série de composants imprimés, en l’occurrence des montures de lunettes. Le produit brut est retiré du récipient, dépoussiéré et peaufiné en le ponçant par exemple et en le colorant.
Moins de déchets
La méthode existe depuis un certain temps déjà. Alors qu’avant, les composants étaient encore rendus solidaires les uns aux autres au moyen de pièces intermédiaires (‘supports’) lors de la fabrication, la technologie a entre-temps évolué vers moins de déchets résiduels et davantage d’efficience. Grâce à des améliorations dans le logiciel, toujours plus de composants sont placés dans le récipient, façon Tetris, ce qui diminue la quantité de poudre utilisée.
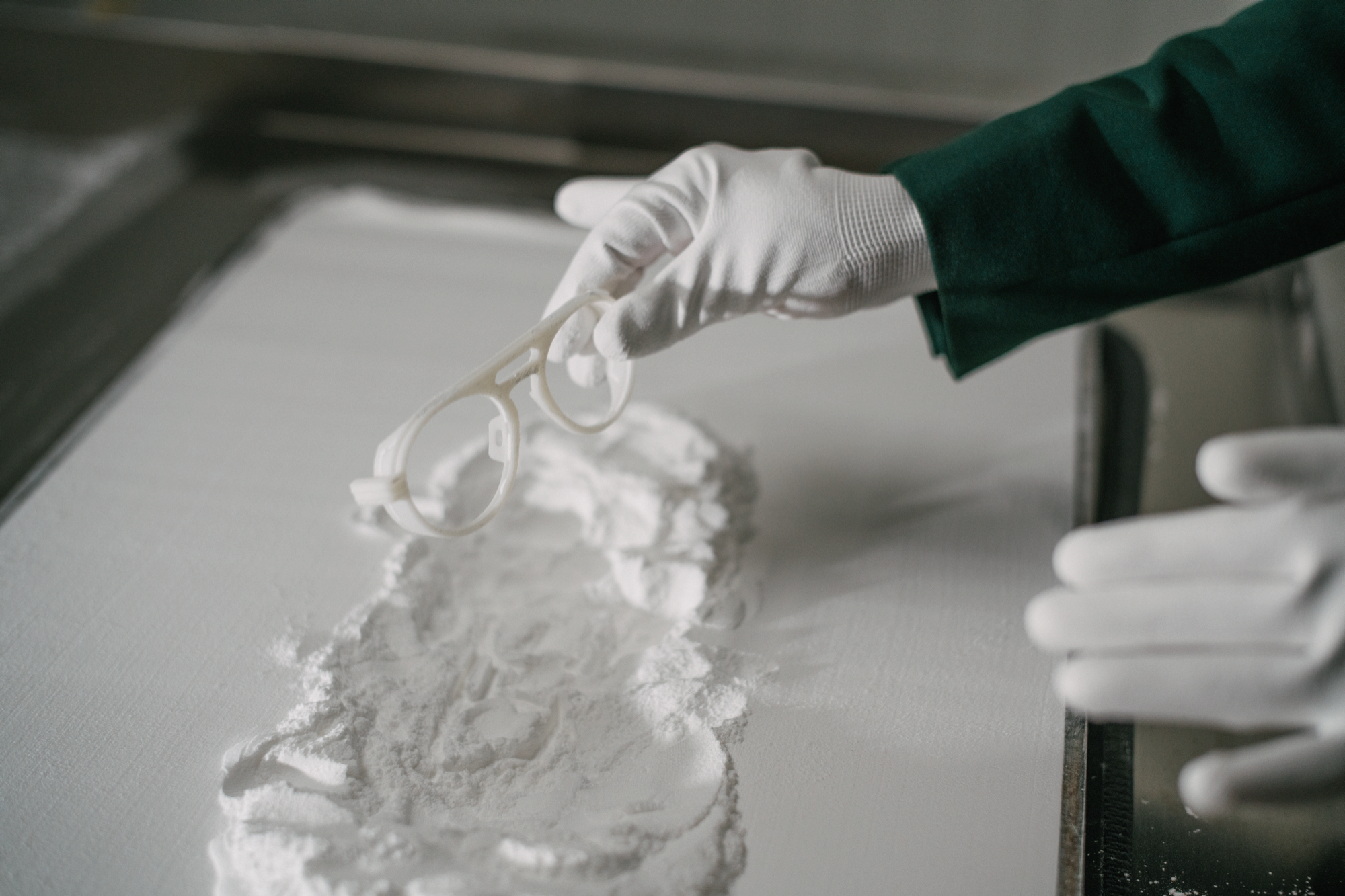
La poudre non fondue est à son tour de nouveau employée, selon Laudus: ‘Mais elle devient obsolète et ne peut donc pas être réutilisée indéfiniment. Voilà pourquoi nous avons chez Materialise mis au point la technologie BlueSynth, qui permet quand même dans certaines machines de produire encore de bons éléments avec de l’ancienne poudre.’
Logiciels
Ce dernier point est le résultat d’une collaboration avec le département software, car l’entreprise s’est ces dernières années focalisée aussi sur le développement de programmes d’exploitation pour imprimantes 3D.
‘Nous nous y sommes lancés, afin de mieux piloter nos imprimantes, mais la technologie est à présent devenue un produit commercial’, signale Laudus. Materialise fournit à présent aussi un logiciel aux autres entreprises disposant une imprimante 3D. ‘Il est question ici de préparer les données à imprimer’, poursuit-il. ‘Mais nous proposons aussi un logiciel de pilotage de la machine, afin de trouver le trajet le plus efficient que le rayon laser doit parcourir par exemple. On réduit toujours plus la distance avec la machine.’ Ce sont là de petits pas en avant destinés à rendre le système toujours plus efficient et durable.