La zone industrielle de Louvain accueille la seule entreprise belge cotée au Nasdaq. Depuis quelques années déjà, l’entreprise y est spécialisée en fabrication additive ou impression 3D.
Ne vous y trompez pas : Materialise ne commercialise pas d’imprimantes 3D. L’entreprise fabrique sous contrat, développe des logiciels, supporte des développeurs de produits, etc. La mode lancée voici une dizaine d’années, affirmant que tout serait désormais imprimé en 3D, est passée. Mais il ne s’agit pas forcément d’une évolution négative, estime Bart Van der Schueren, son CTO.
« Le secteur est dans une situation remarquable, ceci en raison des apports financiers gigantesques. L’émergence de ChatGPT et de l’IA générative en général se traduit par un afflux d’investissements. Beaucoup d’argent a été investi ces dernières années dans la fabrication additive, mais souvent par des personnes ayant des idées saugrenues et sans plan commercial. À présent que les fonds se tarissent quelque peu, certaines activités disparaissent à nouveau. Mais l’avantage principal d’une telle situation est que les activités à valeur ajoutée reprennent le dessus. Il faut pouvoir offrir une plus-value économique. »
« L’avantage est désormais plus clair. Nous avons lancé l’an dernier une enquête auprès de quelque 300 entreprises de production qui ne sont pas clientes chez nous. Elles connaissent la fabrication additive, veulent la mettre en œuvre et en comprennent les potentialités : démarrage plus rapide, liberté de forme, pas d’investissement initial dans des outils de production. Ces avantages sont aujourd’hui connus de nombreuses entreprises. »
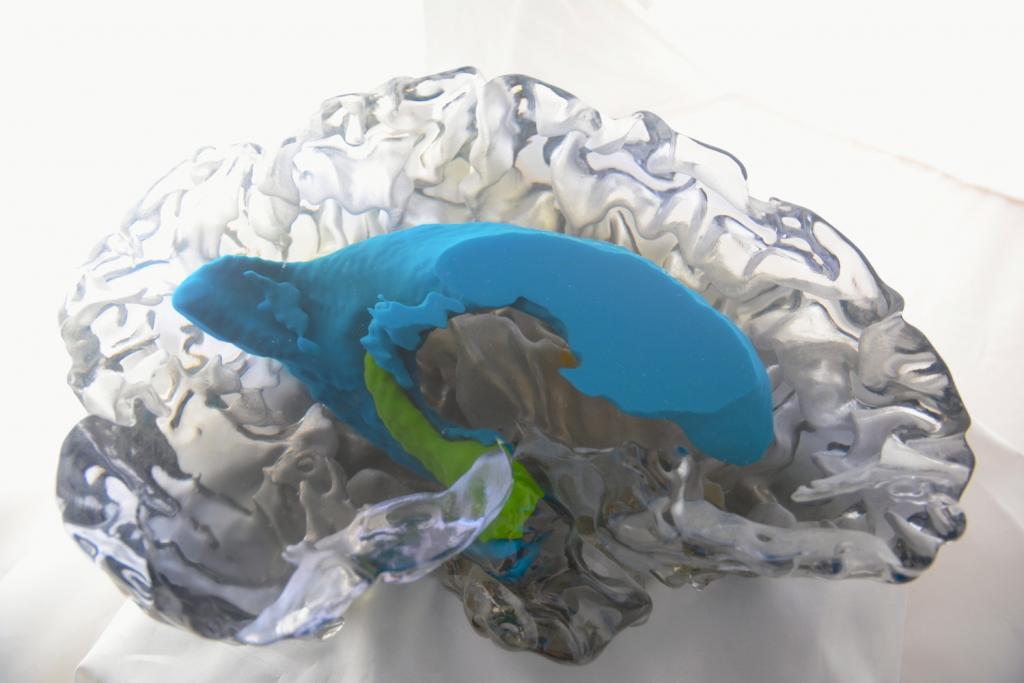
A titre d’exemple, Van der Schueren cite les appareils auditifs. « Dans ce secteur, la fabrication additive connaît un vif succès et apparaît comme une tendance de fond pour fabriquer un appareil sur mesure. » Mais au-delà de ces niches également (officieusement, nous entendons citer plusieurs noms de multinationales industrielles connues), certains commencent à se demander si la prochaine génération d’appareils ne pourra pas être plus efficacement fabriquée en impression 3D, et pas uniquement les prototypes.
Le domaine où l’impression 3D a véritablement décollé est celui des applications médicales. Van der Schueren : « Dans ce secteur, personne ne doute de l’importance croissante que prendra la fabrication additive. C’est d’ailleurs à ce niveau que Materialise peut proposer une valeur ajoutée importante. Vous faites un scan d’une personne, ou d’une partie du corps de cette personne, et vous pouvez concevoir une anatomie avant de l’imprimer sous forme d’implant. Mais nous pouvons également proposer des outils qui seront utilisés durant une opération. »
L’autre volet majeur est l’activité industrielle où Materialise joue sur deux tableaux. D’une part, imprimer pour des tiers en analysant s’il est pertinent et évolutif de produire pour des clients qui le demandent et ne veulent pas réaliser eux-mêmes l’investissement nécessaire. « Il s’agit d’un marché d’externalisation qui nous permet d’améliorer nos propres connaissances. » L’autre pilier concerne les logiciels, surtout à destination d’entreprises qui réinternalisent l’impression 3D. « Beaucoup estiment que c’est important de travailler en interne d’un point de vue stratégique. Nous leur proposons alors notre savoir-faire sous la forme d’outils logiciels notamment. » Désormais, quelque 20% du chiffre d’affaires de Materialise sont générés par le développement de logiciels, le reste provenant de la production proprement dite, les composants médicaux étant le moteur principal.
Matériel et logiciel pour le corps humain
Fin 2023, Materialise faisait la une de l’actualité, notamment dans le cadre de la transplantation d’un œil aux États-Unis où l’entreprise proposait différents outils sur mesure pour le donneur et le patient, y compris un modèle 3D pour préparer les chirurgiens de manière virtuelle. « Ce projet était particulièrement intéressant dans la mesure où il nous permet d’appliquer notre technologie la plus avancée dans un cadre exceptionnel. Cela nous permet de faire la différence sur le plan technologique », considère Pieter Slagmolen, Innovation manager Medical chez Materialise. Plus la technologie s’affine, plus elle peut être déployée en dehors du domaine médical spécifique.
« L’automatisation, l’IA et l’amélioration des logiciels nous permet de ne plus devoir nous limiter aux 2 à 3 patients par an pour des cas particuliers, mais à pouvoir aussi aider le patient classique, par exemple pour une opération de l’épaule. » Désormais d’ailleurs, l’entreprise traite chaque année plus de 55.000 patients, au-delà des cas spéciaux. En outre, Materialise a déjà analysé plus de 6 millions de scans de patients.
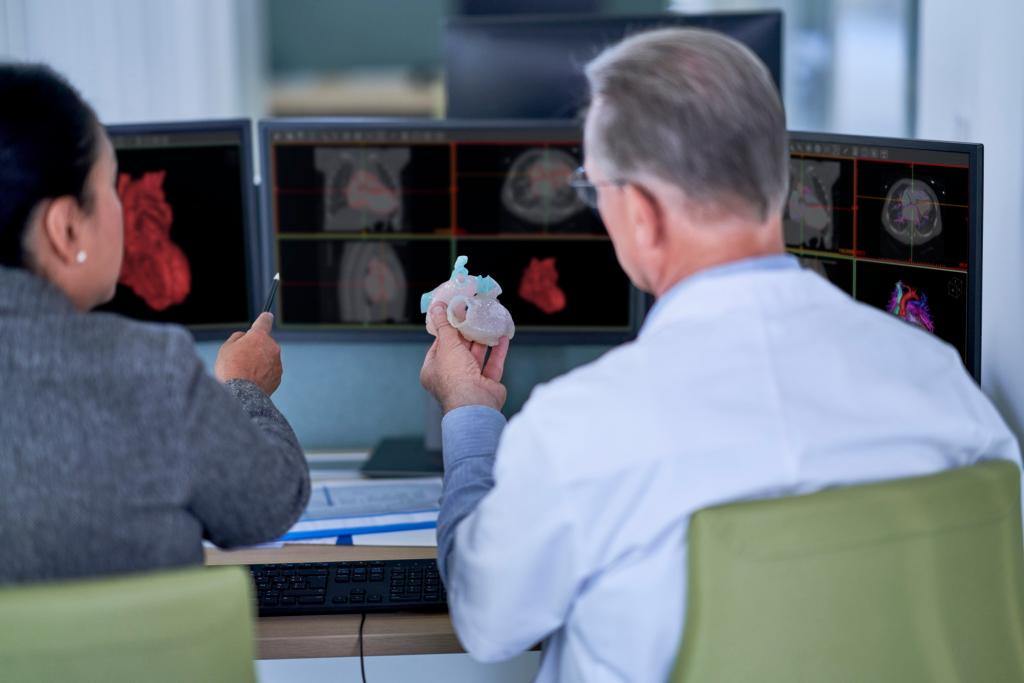
En l’occurrence, le défi est que la technologie doit maintenant être suffisamment mature pour être déployée dans un environnement clinique. Or le choix du matériel joue aussi un rôle majeur.« Pour les implants, il s’agit souvent du titane, mais il existe aussi des systèmes qui utilisent du plastique biocompatible. Mais nous regardons aussi d’autres domaines. C’est ainsi qu’en 2015, nous étions la première entreprise au monde à fournir des produits de série pour Airbus et leur A350. »
C’est sur cette base qu’une série de matériaux ont été développés pour la biologie, et notamment des implants. « Nous en sommes encore à la phase de R&D et des premières applications cliniques et tout n’est pas applicable partout. En outre, lorsqu’un implant disparaît, il faut pouvoir trouver quelque chose qui remplace cette fonction. »
Plus tôt dans l’année, Materialise a reçu l’agrément de la FDA américaine pour le lancement d’un premier essai clinique sur 30 enfants ayant une attelle. Il s’agissait d’un petit tube placé à l’extérieur de la trachée d’un nouveau-né souffrant d’une affection particulière où la trachée se referme. « Ils sont reliés à un système de ventilation, mais étant donné qu’ils grandissent très vite, il n’est pas possible d’utiliser du métal. Nous nous intéressons donc à des matériaux résorbables et avons reçu l’autorisation de poursuivre nos travaux aux États-Unis. »
L’activité médicale de Materialise ne se concentre dès lors pas sur des pièces standards en grand volume. « Nous nous concentrons sur le travail sur mesure pour des appareils et des services personnalisés. Souvent, il n’est pas question d’objets, mais de logiciels qui nous permettent de mieux nous positionner. L’objectif ultime est de réaliser des gains d’efficacité et d’offrir un système durable. Cela étant, nous constatons que l’impression 3D gagne aussi du terrain dans le monde médical pour la réalisation d’équipements standards, ne serait-ce que parce qu’il s’agit souvent de quantités plus petites que dans d’autres secteurs. »
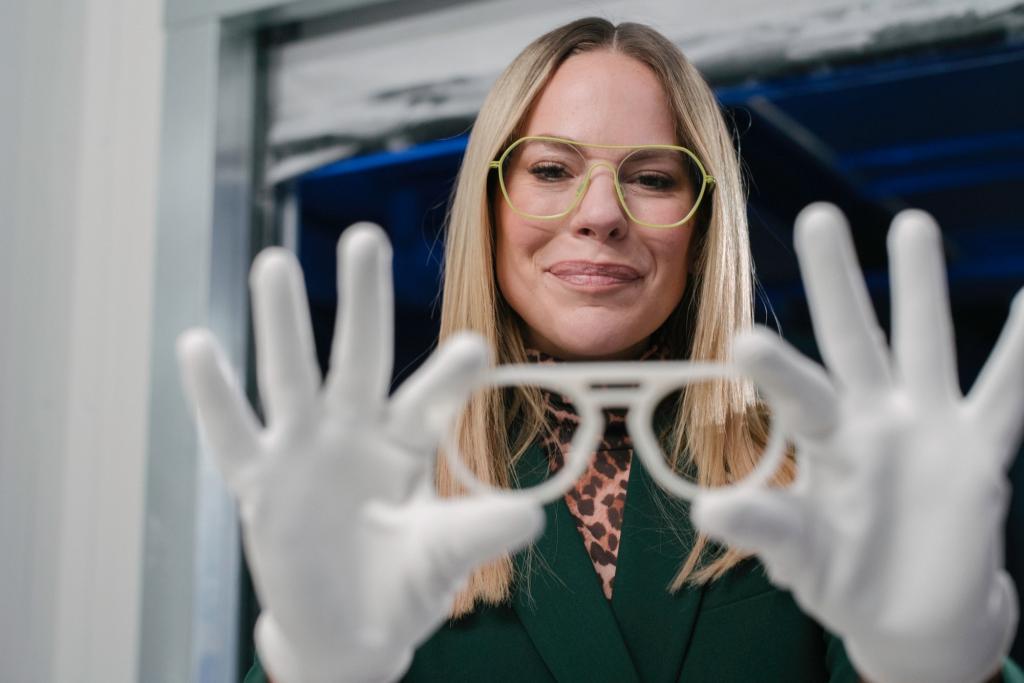
L’idée sous-jacente de l’évolution vers les logiciels est que le marché des équipements et services personnalisés est nettement plus grand que ce que Materialise peut offrir. « Nous le faisons depuis longtemps dans les hôpitaux où nous pouvons proposer des services similaires grâce à nos outils, mais aussi dans le monde industriel. Or avec l’évolution technologique autour de l’IA et du cloud, nous disposons désormais de l’ensemble des pièces du puzzle pour passer d’une image médicale à un implant qui sera posé chez le patient. »
En l’occurrence, le rôle du cloud n’est pas à sous-estimer dans la mesure où une image médicale peut désormais être convertie en un implant imprimé. « Le travail technique est assuré par des algorithmes et des ingénieurs et le volet clinique par des médecins, tandis que le cloud prend en charge les interactions entre ces deux mondes qui travaillent souvent en pratique sur des sites différents. En outre, la production se fait en général aussi dans des lieux différents. « Dans ce cas, un environnement cloud performant est un facilitateur, souligne Slagmolen. Mais aussi dans la solution finale : un médecin souhaite une interface différente de celle de l’ingénieur qui effectue le travail préparatoire, même s’ils utilisent une seule et même couche de données. Il en résulte un continuum efficace qui pourra se révéler à terme aussi efficace que si l’on utilisait une solution standard du marché. »
« Les apportsfinanciers sont gigantesques. L’émergence de ChatGPT se traduit par un afflux d’investissements. »
En d’autres termes, le département médical de Materialise ne se limite pas à de l’impression, pour couvrir également de la planification préopératoire par exemple. « Nombre de nos activités sont purement liées aux logiciels. Ainsi, nous aidons le médecin en ajoutant de l’information à son intervention. Par exemple en indiquant où il faut percer pour placer une broche, ou encore à quel endroit installer une vis. Il s’agit là d’informations que nous fournissons lors de la préparation, mais que le médecin ne trouvera pas aussi facilement. »
Du prototype à la production
Cela étant, la fabrication additive se prête aussi parfaitement au prototypage. C’est le domaine pris en charge par Jurgen Laudus, vice-président Manufacturing chez Materialise, spécialisé dans les prototypes uniques et les petites productions en série. « A ce stade, nous travaillons surtout la lunetterie, la chaussure, l’aérospatial, le tooling, etc. », précise Laudus.
Dans ce segment, Materialise se positionne comme l’un des principaux acteurs . Ainsi, si un constructeur automobile veut tester un nouveau pare-chocs ou tableau de bord, il y a des grandes chances que la société louvaniste fabrique le premier produit physique. « Souvent, un prototype sert également de point de départ d’une petite production en série. L’aérospatial est ainsi l’un des secteurs ayant la plus forte croissance dans le monde industriel. » C’est ainsi que dès 2015, Materialise a été l’une des premières entreprises au monde à fournir des produits de série pour l’A350. « Nous continuons à les livrer mais entre-temps, d’autres fournisseurs d’Airbus nous ont rejoint et nous leur fournissons toujours plus de produits. »
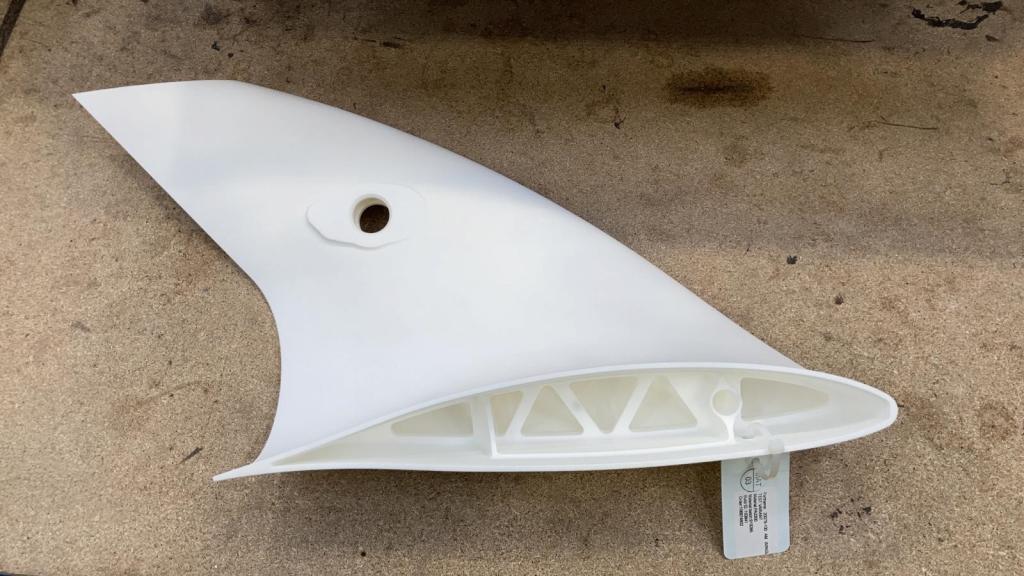
Le problème se pose lorsqu’une production devient trop importante pour être réalisée en impression 3D. « Il est clair que dès qu’une série devient trop importante, l’impression 3D n’est probablement plus aussi intéressante », reconnaît Laudus. Mais de souligner que certains produits commercialisés ne sont pas forcément des produits de masse. L’un des défis de la technologie consiste à faire baisser le coût total. Aujourd’hui, on se concentre sur des petites séries, ce qui est parfait dans le monde aéronautique. Mais dans l’automobile, on se retrouve avec de grands volumes, ce qui devrait idéalement faire baisser les prix.» Ce qui n’est pas impossible, selon Laudus. «Plus un processus est rapidement sou contrôle, plus il doit être possible de diminuer les coûts. »
Précisons que lorsque Materialise évoque de petites quantités, il s’agit toutefois de plusieurs dizaines de milliers d’unités. « C’est ainsi que pour l’A350, nous avons entre-temps fabriqué 120.000 pièces. Certes, il s’agit de plusieurs designs différents. La question clé est de savoir s’il y a un business case. Pour des pièces très complexes, c’est relativement facile à trouver. Les entreprises ne se contentent pas de regarder simplement le coût de production, mais aussi le coût du stockage, les risques liés à un fournisseur trop distant, etc. C’est pour de tels acteurs que nous fabriquons des produits dont les volumes peuvent atteindre des dizaines de milliers d’unités. »
Materialise en chiffres
256millions d’euros (2023)
2.400 collaborateurs